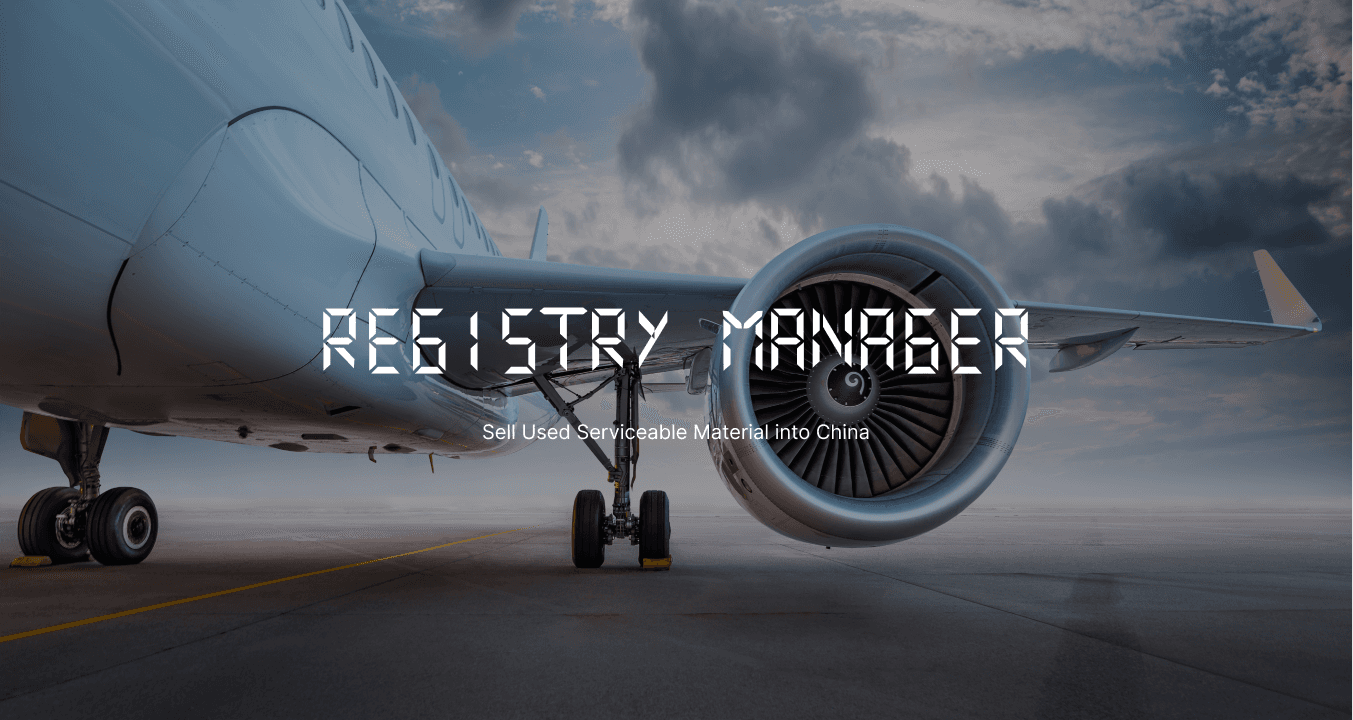
Project Overview
The Registry Manager is a module on the Block Aero platform that helps regulators and oversight organizations standardize aviation processes and manage detailed asset records. It provides easy access to asset information within the registry, publication status, historical data, and related documents.
Discovery
Definition
Ideation
Solution
High Fidelity Designs
Registry Manager
UX Design
Block Aero
Dec 2023 - Oct 2024
Challenges
Establishing a USM (Used Serviceable Material) parts registry that meets the compliance needs of the Chinese Civil Aviation Authority (CAAC) involves several challenges:
Regulatory Alignment: The CAAC has specific regulations and standards that may differ from those of other aviation authorities, such as the FAA. Ensuring that the USM parts registry aligns with these requirements can be complex.
Documentation and Traceability: The CAAC requires rigorous documentation and traceability for all aviation parts. Developing a system that can accurately track the history and condition of used parts can be challenging.
Quality Assurance Standards: Meeting the CAAC's quality assurance requirements for used parts necessitates implementing strict inspection and testing protocols, which may differ from those used in other jurisdictions.
Certification and Approval Processes: Gaining recognition and approval from the CAAC for a USM registry may involve navigating a lengthy certification process, which can be resource-intensive.
Cultural and Communication Barriers: Differences in business practices, language, and regulatory understanding between US and Chinese entities can create challenges in compliance and partnership.
Market Acceptance: Gaining acceptance among Chinese operators and manufacturers for using USM parts may require educational efforts and demonstrations of safety and reliability.
Logistical Issues: Coordinating the logistics of sourcing, storing, and distributing USM parts in compliance with CAAC regulations may present logistical challenges.
Legal and Liability Concerns: Understanding and navigating the legal implications of using USM parts in China, including liability issues, is critical for compliance.
Data Security and Privacy: Ensuring that the registry complies with both US and Chinese data protection laws can be complex, especially when sharing information across borders.
Continuous Monitoring and Updates: The regulatory landscape can change, necessitating ongoing updates to the registry to ensure continued compliance with CAAC requirements.
Discovery
The discovery phase of designing a registry to meet the Chinese Civil Aviation Authority (CAAC) requirements involves several critical steps to ensure that the system is compliant, efficient, and effective. Here’s a breakdown of the process:
1. Stakeholder Engagement
Identify Stakeholders: Engage with key stakeholders, including regulatory bodies, airlines, maintenance organizations, and parts suppliers.
Gather Requirements: Conduct interviews, surveys, and workshops to understand their needs, concerns, and expectations regarding the registry.
2. Regulatory Analysis
Study CAAC Regulations: Analyze the specific regulations and standards set by the CAAC concerning used serviceable materials (USM).
Compare with Other Regulations: Understand how CAAC regulations align or differ from those of other aviation authorities (e.g., FAA, EASA).
3. Existing Systems Review
Benchmarking: Research existing registries and systems used in other jurisdictions or industries that comply with similar regulatory frameworks.
Identify Best Practices: Gather insights on successful features, processes, and technologies from these systems.
4. Gap Analysis
Identify Compliance Gaps: Compare current capabilities with CAAC requirements to identify gaps in documentation, traceability, quality assurance, and data management.
Prioritize Needs: Assess which gaps are most critical to address in the registry design.
5. Technical Feasibility Assessment
Evaluate Technology Options: Explore potential technologies and platforms that can support the registry, including database management systems, blockchain for traceability, and user interfaces.
Assess Integration Needs: Determine how the new registry will integrate with existing systems used by stakeholders.
6. Data Requirements Definition
Determine Data Elements: Define the necessary data fields for the registry, such as part identification, condition, maintenance history, and certification status.
Data Standards: Establish data standards and formats that ensure consistency and compatibility across different users and systems.
7. Risk Assessment
Identify Risks: Analyze potential risks associated with the registry, including data security, compliance failures, and operational challenges.
Mitigation Strategies: Develop strategies to mitigate identified risks, ensuring the registry's robustness and reliability.
8. Prototype Development
Create Initial Designs: Develop wireframes or mockups of the registry interface and workflows based on the gathered requirements and identified gaps.
Feedback Loop: Present prototypes to stakeholders for feedback and iterate based on their input.
9. Roadmap Creation
Implementation Plan: Outline a roadmap for development, including phases, timelines, and milestones.
Resource Allocation: Identify the resources needed (e.g., personnel, technology) to move forward with the design and implementation.
10. Documentation
Compile Findings: Document all findings, requirements, and decisions made during the discovery phase.
Create a Reference Guide: Develop a guide that can be used throughout the design and implementation phases to ensure alignment with CAAC requirements.
Pain Points
Aircraft fleet recycling companies face several pain points when selling Used Serviceable Material (USM) into China:
1. Regulatory Compliance
Complex Regulations: Navigating the CAAC's regulations can be challenging, as they may differ significantly from those in other countries.
Certification Requirements: Obtaining necessary certifications for USM parts can be time-consuming and resource-intensive.
2. Documentation and Traceability
Demand for Rigorous Documentation: Chinese authorities require extensive documentation for the history and condition of USM parts, which can be difficult to compile and verify.
Record Keeping: Maintaining accurate and comprehensive records over the lifecycle of parts adds to operational complexity.
3. Quality Assurance Standards
Meeting High Standards: USM must meet stringent quality assurance standards set by the CAAC, which may require additional testing or certification processes.
Perception of Quality: Overcoming skepticism regarding the reliability of USM compared to new parts can be a barrier to market acceptance.
4. Logistical Challenges
Shipping and Customs: Exporting USM to China involves navigating complex shipping logistics and customs regulations, which can lead to delays and additional costs.
Handling and Storage: Ensuring proper handling and storage conditions during transit to maintain part quality can be challenging.
5. Market Acceptance
Cultural Differences: Differences in business practices and attitudes towards used parts can hinder market penetration.
Trust Issues: Building trust with Chinese operators and airlines regarding the safety and reliability of USM can take time.
6. Competition
Local Alternatives: Competing with local suppliers who may have established relationships and a better understanding of the market can be difficult.
Price Sensitivity: Price competition can limit margins, especially if local suppliers offer lower prices for similar parts.
7. Data Security and Privacy
Data Sharing Concerns: Concerns about data security and compliance with both US and Chinese data protection laws can complicate transactions.
Transparency Requirements: Providing transparent data while protecting proprietary information can be a delicate balance.
8. Economic and Political Factors
Trade Relations: Fluctuating trade relations between the US and China can impact market access and regulatory environments.
Economic Conditions: Broader economic factors, such as currency fluctuations and market demand, can also affect sales.
Problem Statement
The current challenges faced by aircraft fleet recycling companies in selling Used Serviceable Material (USM) into China—stemming from complex regulatory compliance, stringent documentation and traceability requirements, quality assurance standards, logistical hurdles, and market acceptance—hinder the efficient and effective integration of USM into the Chinese aviation market. To address these pain points, a comprehensive registry must be designed that streamlines compliance processes, ensures rigorous documentation, enhances quality verification, facilitates logistical operations, and fosters trust among stakeholders, ultimately enabling smoother transactions and greater market penetration for USM in China.
Definition
Once the documentation for the requirements was finalized, the design team immediately set to work on translating those requirements into a viable solution. This phase involved several key steps:
1. Solution Conceptualization
Brainstorming Sessions: The team organized brainstorming sessions to explore various design concepts that could meet the documented requirements. This collaborative approach encouraged diverse ideas and innovative thinking.
Feasibility Analysis: Each concept was evaluated for feasibility in terms of technology, budget, and timeline. This ensured that only the most practical solutions were considered for development.
2. Detailed Design Specification
Functional Specifications: The team created detailed specifications for each function of the registry, outlining how each feature would operate and interact with users. This included data input methods, reporting capabilities, and user roles.
User Interface (UI) Design: Initial UI mockups were developed to visualize how users would interact with the registry. The team focused on creating an intuitive and user-friendly interface that would facilitate easy navigation and accessibility.
3. Technical Architecture Development
System Architecture: The team designed the technical architecture of the registry, including the database structure, server requirements, and integration points with other systems. This architecture was critical for ensuring that the registry could handle the anticipated data volume and user load.
Technology Stack Selection: Decisions were made regarding the technology stack to be used, including programming languages, frameworks, and cloud services, ensuring alignment with the project’s needs and future scalability.
4. Prototyping
Rapid Prototyping: The design team developed a prototype of the registry to demonstrate key functionalities and gather feedback from stakeholders. This iterative process allowed for real-time adjustments based on user input.
Usability Testing: Initial usability tests were conducted with potential users to identify any pain points or areas for improvement in the design.
5. Iterative Refinement
Feedback Integration: Based on the feedback received during prototyping and usability testing, the team iteratively refined the solution, making adjustments to enhance functionality, usability, and performance.
Validation of Requirements: Throughout this process, the design team continuously validated that the evolving solution remained aligned with the original requirements, ensuring that no critical needs were overlooked.
Onboarding Process
Once the solution had undergone several rounds of iteration, the team recognized the importance of facilitating a smooth onboarding experience for customers using the platform. To achieve this, we decided to create a short, engaging video that would guide users through the onboarding process. I was entrusted with overseeing the entire video production process.
1. Identifying Key Messages
User Needs Assessment: I began by identifying the key points that needed to be communicated to users during the onboarding process. This involved understanding their concerns, questions, and the specific steps they would need to take to onboard their assets effectively.
Outline Creation: After gathering insights from stakeholders and potential users, I developed a clear outline that highlighted the essential elements to cover in the video, ensuring that it would address all critical aspects of the onboarding journey.
2. Script Development
Crafting the Narrative: I wrote a concise and engaging script that conveyed the necessary information in a straightforward manner. The script included clear instructions, tips for navigating the platform, and emphasized the benefits of onboarding their assets.
Incorporating User Scenarios: To enhance relatability, I included real-world scenarios that potential users might encounter, demonstrating how the platform could simplify their processes.
3. Visual Planning
Storyboard Creation: I developed a storyboard to visually map out each scene of the video. This helped in visualizing how the narrative would unfold and ensured that the visuals aligned with the script.
Selecting Visual Elements: I chose graphics, animations, and screenshots of the platform that would enhance understanding and engagement. The goal was to make the video visually appealing while effectively communicating the onboarding steps.
4. Production Process
Video Recording: I coordinated the recording of voiceovers and any on-screen demonstrations needed for the video. I ensured that the tone was friendly and professional to create a welcoming atmosphere for users.
Editing: During the editing phase, I meticulously pieced together the visuals, voiceovers, and background music to create a cohesive and engaging narrative. I focused on maintaining a brisk pace to keep viewers engaged while ensuring clarity.
5. Feedback and Revisions
Internal Review: Once a draft of the video was completed, I shared it with team members and stakeholders for feedback. Their insights helped identify areas for improvement and clarification.
Final Edits: Based on the feedback received, I made necessary revisions to enhance the video’s effectiveness and ensure it met our communication goals.
6. Launch and Distribution
Publishing the Video: After finalizing the video, I collaborated with the marketing team to determine the best platforms for distribution, ensuring it would reach our target audience effectively.
Promotion: We created a plan to promote the video as part of our onboarding materials, including integrating it into the platform itself and sharing it through email campaigns and social media.
By taking charge of the video production process, I was able to create a valuable resource that not only simplifies the onboarding experience for customers but also enhances their understanding of the platform. This initiative aimed to build confidence in users as they navigated the onboarding process, ultimately fostering a smoother transition and encouraging successful asset integration.
Solution
Designing a registry to meet the requirements of the Chinese Civil Aviation Authority (CAAC) involves creating a comprehensive and user-friendly system that ensures compliance, traceability, and efficiency for managing Used Serviceable Material (USM). Here’s a detailed outline of the solution:
1. System Architecture
Cloud-Based Platform: Utilize a cloud infrastructure to ensure scalability, data security, and accessibility for users across different locations.
Modular Design: Implement a modular architecture to allow for future enhancements and integration with other systems.
2. User Interface (UI) and User Experience (UX)
Intuitive Dashboard: Design a user-friendly dashboard that provides a clear overview of key metrics, recent activities, and alerts regarding compliance status.
Guided Navigation: Include step-by-step wizards to assist users in navigating the system for tasks such as asset onboarding, documentation submission, and reporting.
3. Data Management
Comprehensive Data Fields: Include fields for essential data such as part identification, maintenance history, certification status, and condition assessments.
Standardized Formats: Use standardized data formats and terminology to ensure consistency and facilitate data sharing with regulatory authorities.
4. Documentation and Traceability
Integrated Document Management: Implement a document management system that allows users to upload, store, and manage all necessary documentation related to USM parts (e.g., maintenance records, certifications).
Audit Trail: Create a robust audit trail feature that logs all actions taken on parts within the registry, ensuring full traceability for regulatory compliance.
5. Compliance Features
Automated Compliance Checks: Develop automated compliance checklists that guide users through necessary regulatory requirements for each USM part, ensuring that all criteria are met before onboarding.
Alerts and Notifications: Set up alerts for upcoming compliance deadlines, document expirations, or any changes in regulatory requirements that may affect the status of USM.
6. Quality Assurance and Verification
Quality Control Protocols: Incorporate features for defining and managing quality assurance protocols, including inspection and testing requirements for USM parts.
Certification Management: Enable users to manage and track certification statuses, including reminders for renewals or updates.
7. Reporting and Analytics
Customizable Reports: Provide tools for generating customizable reports on USM inventory, compliance status, and audit findings to facilitate data analysis and decision-making.
Analytics Dashboard: Implement analytics features to track trends and performance metrics, aiding in proactive management of USM assets.
8. Integration Capabilities
Interoperability: Ensure the registry can integrate with existing systems used by airlines, maintenance organizations, and regulatory bodies for seamless data exchange.
API Access: Provide API access for third-party developers to create additional functionalities or connect to other software systems as needed.
9. User Training and Support
Comprehensive Training Materials: Develop user manuals, video tutorials, and FAQs to assist users in understanding how to navigate and utilize the registry effectively.
Customer Support: Offer robust customer support channels, including chat, email, and phone support, to address user inquiries and technical issues promptly.
10. Security and Compliance
Data Security Protocols: Implement strong security measures, including encryption, user authentication, and role-based access control to protect sensitive data.
Regular Audits: Conduct regular audits of the registry system to ensure compliance with CAAC regulations and industry standards.
Conclusion
This registry solution aims to create a streamlined, efficient, and compliant system for managing USM parts, addressing the specific needs of the CAAC while enhancing the overall user experience. By focusing on data management, traceability, compliance, and user support, the registry can facilitate smoother transactions and foster confidence among stakeholders in the aviation industry.
Summary
A registry designed to meet CAAC requirements offers significant benefits for aviation stakeholders by streamlining the management of Used Serviceable Material (USM).Key Benefits:
Enhanced Compliance: The registry automates compliance checks and maintains comprehensive documentation, ensuring stakeholders can easily meet regulatory requirements, thereby reducing the risk of penalties or operational disruptions.
Improved Traceability: With robust data management and audit trail features, stakeholders can track the history and condition of USM parts, fostering transparency and trust throughout the supply chain.
Efficiency and Cost Savings: The user-friendly interface and guided workflows simplify the onboarding process for assets, reducing time and labor costs associated with manual tracking and documentation.
Quality Assurance: Integrated quality control protocols help ensure that all USM parts meet safety and reliability standards, enhancing the overall safety of operations.
Data-Driven Insights: Reporting and analytics capabilities provide stakeholders with valuable insights into inventory management, compliance status, and operational performance, enabling informed decision-making.
By centralizing information and facilitating collaboration among airlines, maintenance organizations, and regulatory bodies, the registry enhances operational efficiency and safety in the aviation industry.